Virtual Product Development Laboratory (VP)
Here you can learn how to use CATIA, Solid Works and CIM Database on a total of 12 computers.CATIA is a CAx system solution. It enables the design of 3D geometries (CAD) and has additional functionalities, such as the simulation of static load cases using the finite element method (CAE) or the development of milling programs (CAM). The focus is on geometry generation. Furthermore, the PDM software CIM-Database is used in the exercise. Among other things, this is responsible for controlling the workflow or data management. Furthermore, the students learn about functionalities such as version and variant management as well as role and rights management in the modern product development process.
Here you can learn how to use CATIA, Solid Works and CIM Database on a total of 12 computers.CATIA is a CAx system solution. It enables the design of 3D geometries (CAD) and has additional functionalities, such as the simulation of static load cases using the finite element method (CAE) or the development of milling programs (CAM). The focus is on geometry generation. Furthermore, the PDM software CIM-Database is used in the exercise. Among other things, this is responsible for controlling the workflow or data management. Furthermore, the students learn about functionalities such as version and variant management as well as role and rights management in the modern product development process.
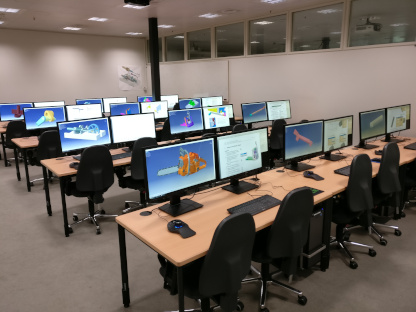
VR Lab
A 12m² greenroom with HTC-Vive VR goggles for the use of Roomscale in research. It enables the position and orientation of the user’s head and hands to be determined at a sampling rate of 90Hz with a repeatability of 0.3mm. Furthermore, two powerful computers can be used to work on VR environments with the aid of the Unity engine. Areas of application include early product influence in the design process during the concept phase, 3D sketching, direct manipulation of spatial conditions in assembly, workplace design, and visualization of different assembly sequences or the structure of products and assembly planning.
A 12m² greenroom with HTC-Vive VR goggles for the use of Roomscale in research. It enables the position and orientation of the user’s head and hands to be determined at a sampling rate of 90Hz with a repeatability of 0.3mm. Furthermore, two powerful computers can be used to work on VR environments with the aid of the Unity engine. Areas of application include early product influence in the design process during the concept phase, 3D sketching, direct manipulation of spatial conditions in assembly, workplace design, and visualization of different assembly sequences or the structure of products and assembly planning.
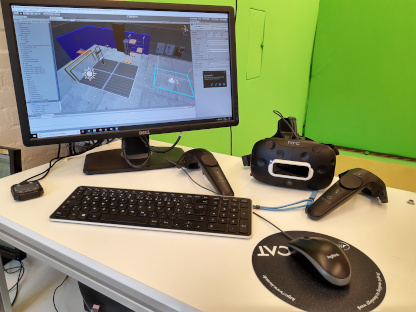
Mechatronics Lab
In the mechatronics laboratory there is an automatic placement machine as well as a convection reflow oven. The SMD placement system M10V can be used for the creation of prototypes and small series. The placement system has the following options: Fully automatic placement, Automatic registration mark correction and PCB detection, Extra small footprint, Operation also possible without feeder, Easy processing of bulk material, Automatic change of nozzles and TEACH-IN programming or CAD transfer.
The Mistral 260 convection reflow oven has the following specifications: Integrated thermal sensor for temperature measurement on board, USB stick with macro file for evaluation of soldering profiles on PC, Process chamber length: 860 mm, Throughput height: max. 20 mm, Usable soldering width: 260 mm, Heating time: approx. 15 min, Heating zones: 3, Microprocessor controlled oven, Integrated melting point monitoring and graphic representation of the soldering curve on the display.
In the mechatronics laboratory there is an automatic placement machine as well as a convection reflow oven. The SMD placement system M10V can be used for the creation of prototypes and small series. The placement system has the following options: Fully automatic placement, Automatic registration mark correction and PCB detection, Extra small footprint, Operation also possible without feeder, Easy processing of bulk material, Automatic change of nozzles and TEACH-IN programming or CAD transfer.
The Mistral 260 convection reflow oven has the following specifications: Integrated thermal sensor for temperature measurement on board, USB stick with macro file for evaluation of soldering profiles on PC, Process chamber length: 860 mm, Throughput height: max. 20 mm, Usable soldering width: 260 mm, Heating time: approx. 15 min, Heating zones: 3, Microprocessor controlled oven, Integrated melting point monitoring and graphic representation of the soldering curve on the display.
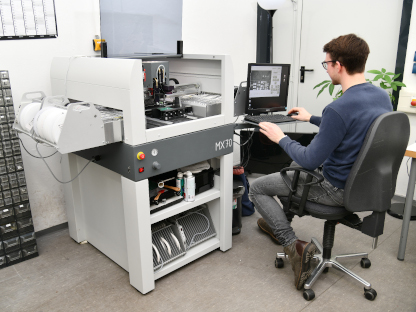
Laboratory for additive manufacturing
For the rapid provision of prototypes and for training students in additive manufacturing processes, three FDM and one SLA printers are available at the Chair of Machine Elements and Computer Aided Product Development. Special features in the SLA printing process include: Multi-color resin, high-temperature resin, elastomeric resin, and UV curing chamber.
The FDM printing process allows a maximum printing area of 330x240x300mm as well as a washable support material (dual extruder) and the following available materials: PLA, ABS, PC, PETG. In addition, a CNC milling machine can be used.
For the rapid provision of prototypes and for training students in additive manufacturing processes, three FDM and one SLA printers are available at the Chair of Machine Elements and Computer Aided Product Development. Special features in the SLA printing process include: Multi-color resin, high-temperature resin, elastomeric resin, and UV curing chamber.
The FDM printing process allows a maximum printing area of 330x240x300mm as well as a washable support material (dual extruder) and the following available materials: PLA, ABS, PC, PETG. In addition, a CNC milling machine can be used.
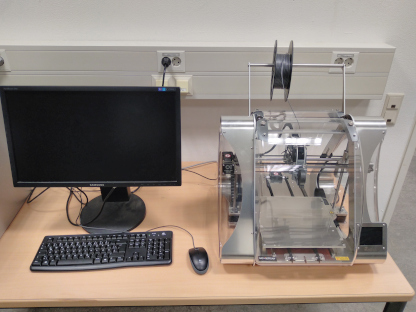
Servo-hydraulic test facility
The Professorship of Machine Elements and Computer Aided Product Development has an extensively equipped servo-hydraulic test field. This consists of various test benches with servo-hydraulic test cylinders, which are used to excite components or complete test setups. Test forces from 10kN to 400kN are available for static and dynamic tests, which can also take place under climate simulation. Furthermore, three 2-axis test stands are available for research purposes. In the test field of the MRP, research on the service life of air springs and vehicle components, as well as aircraft components, is carried out in cooperation with external companies. The multidimensional behavior of air springs and the use of activated carbon to increase volume are investigated. In addition, the laboratory equipment includes an extensively equipped workshop area, work and assembly stations, electrical workstations and a tensile compression testing machine from ZwickRoell.
The Professorship of Machine Elements and Computer Aided Product Development has an extensively equipped servo-hydraulic test field. This consists of various test benches with servo-hydraulic test cylinders, which are used to excite components or complete test setups. Test forces from 10kN to 400kN are available for static and dynamic tests, which can also take place under climate simulation. Furthermore, three 2-axis test stands are available for research purposes. In the test field of the MRP, research on the service life of air springs and vehicle components, as well as aircraft components, is carried out in cooperation with external companies. The multidimensional behavior of air springs and the use of activated carbon to increase volume are investigated. In addition, the laboratory equipment includes an extensively equipped workshop area, work and assembly stations, electrical workstations and a tensile compression testing machine from ZwickRoell.
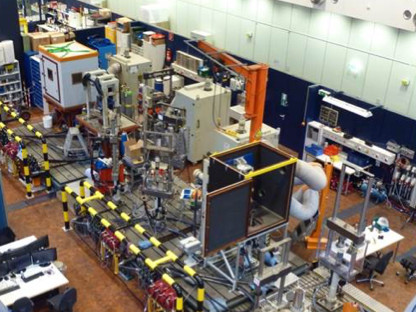
Letzte Änderung: 4. May 2021