Condition assessment of steel infrastructure facilities using multivariate inspection systems and drones
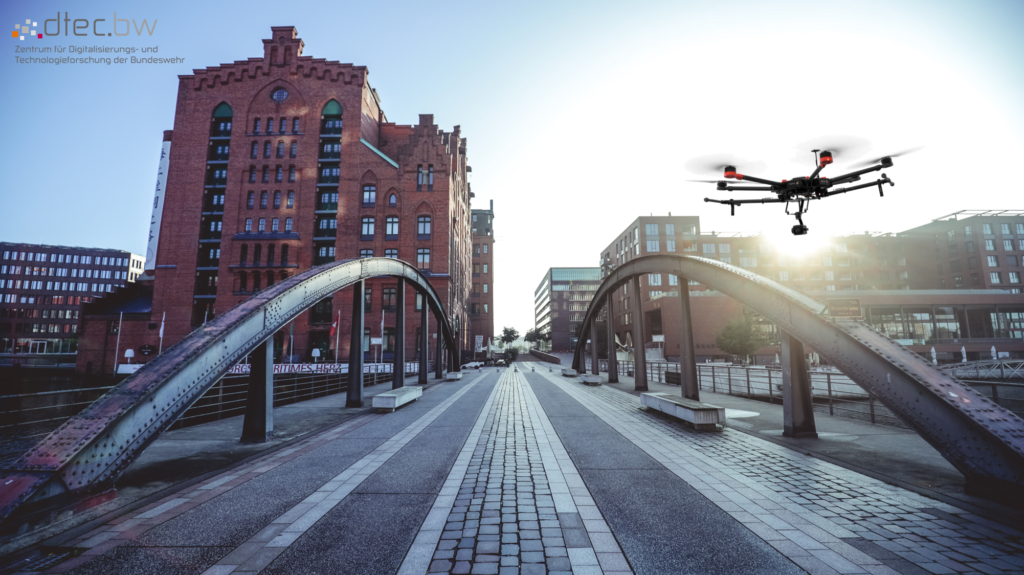
The aim of this project is the method development and testing of an automated multivariate inspection system for steel infrastructure facilities, using UAS as carrier systems. This includes on the one hand the research of the hardware components (including UAS, sensors and units for data acquisition, data processing and data storage) and on the other hand the software components (e.g. algorithms for the optimal flight path and condition analysis based on the sensor data, as well as for storage in a cloud and visualization via web interface). A hyperspectral camera is used as the central sensor for damage detection in order to obtain a multi-layered database for accurate damage analysis during the flight.
At the Chair of Control Engineering the real use of the flight platform is tested in the institute’s own flight cage, with integrated motion capture system. Through the motion capture system, real drone motion can be mapped in a 3D simulation to enable hardware-in-the-loop testing, as well as to investigate different environments and use cases. These include mission planning based on the surface structure of the inspection object, as well as in-flight path finding to avoid collisions and reach target points.
MISDRO is funded by the Center for Digitization and Technology Research of the German Armed Forces (DTEC.Bw). Under the leadership of the Chair of Structural Steel and Hydraulic Steel Engineering, the Chair of Control Engineering and four other industrial partners from the fields of structural inspection, UAS development and AI-based sensor data processing are working on the project.
If you would like to be part of this exciting development process or learn more about this project, feel free to contact Mirco Alpen
Funded by
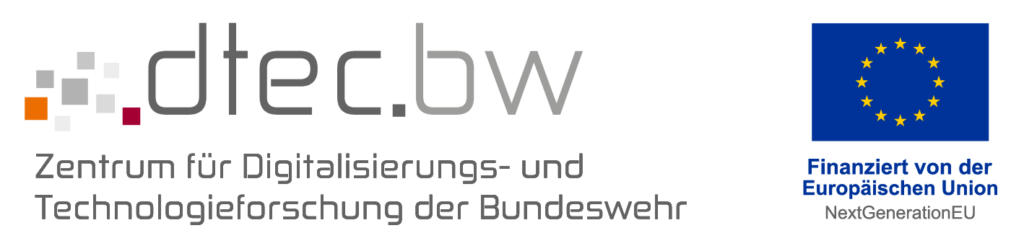
Letzte Änderung: 24. March 2023